Precision is used to express the fineness of the workpiece product. It is a special term for evaluating the geometric parameters of the machined surface. It is also an important indicator for measuring the performance of CNC machining centers. Generally speaking, machining accuracy is measured by tolerance levels. The lower the level, the higher the accuracy. Turning, milling, planing, grinding, drilling, and boring are common processing forms of CNC machining centers. So what processing accuracy should these processing procedures achieve?
1.Turning accuracy
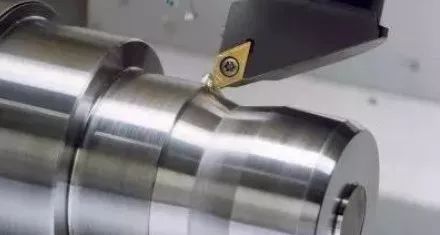
Turning refers to a cutting process in which the workpiece rotates and the turning tool moves linearly or curvedly in a plane to process the internal and external cylindrical surfaces, end faces, conical surfaces, forming surfaces and threads of the workpiece.
The surface roughness of turning is 1.6-0.8μm.
Rough turning requires the use of large cutting depth and large feed rate to improve turning efficiency without reducing the cutting speed. The surface roughness is required to be 20-10um.
For semi-finishing and finishing turning, try to use high speed and smaller feed and cutting depth, and the surface roughness is 10-0.16um.
Finely ground diamond turning tools are used on high-precision lathes to finish turning non-ferrous metal workpieces at high speed with a surface roughness of 0.04-0.01um. This kind of turning is also called "mirror turning".
Xinfa CNC tools have the characteristics of good quality and low price. For details, please visit:
CNC Tools Manufacturers - China CNC Tools Factory & Suppliers (xinfatools.com)
2. Milling accuracy
Milling refers to the use of rotating multi-edged tools to cut workpieces, and is a highly efficient processing method. Suitable for processing planes, grooves, and special surfaces such as splines, gears, and threaded molds.
The general surface roughness of milling processing accuracy is 6.3-1.6μm.
The surface roughness during rough milling is 5-20μm.
The surface roughness during semi-finishing milling is 2.5-10μm.
The surface roughness during fine milling is 0.63-5μm.
3.Planing accuracy
Planing is a cutting processing method that uses a planer to make horizontal and linear reciprocating motions on the workpiece. It is mainly used for the shape processing of parts.
The surface roughness of planing is Ra6.3-1.6μm.
The surface roughness of rough planing is 25-12.5μm.
The surface roughness of semi-finishing planing is 6.2-3.2μm.
The surface roughness of fine planing is 3.2-1.6μm.
4.Grinding accuracy
Grinding refers to a processing method that uses abrasives and abrasive tools to remove excess material from the workpiece. It is a finishing process and is widely used in the machinery manufacturing industry.
Grinding is usually used for semi-finishing and finishing, and the surface roughness is generally 1.25-0.16μm. The precision grinding surface roughness is 0.16-0.04μm.
The surface roughness of ultra-precision grinding is 0.04-0.01μm.
The surface roughness of mirror grinding can reach below 0.01μm.
5. Boring and boring
It is an inner diameter cutting process that uses a tool to enlarge a hole or other circular contour. Its application range generally ranges from semi-roughing to finishing. The tool used is usually a single-edged boring tool (called a boring bar).
The boring accuracy of steel materials can generally reach 2.5-0.16μm.
The processing accuracy of precision boring can reach 0.63-0.08μm.
Post time: Feb-22-2024