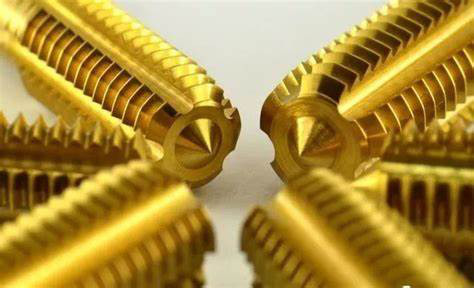
1. The quality of the tap is not good:
Main materials, tool design, heat treatment conditions, machining accuracy, coating quality, etc.
For example, the size difference at the transition of the tap section is too large or the transition fillet is not designed to cause stress concentration, and it is easy to break at the stress concentration during use.
The cross-section transition at the junction of the shank and the blade is too close to the welding port, which leads to the superposition of complex welding stress and the stress concentration at the cross-section transition, resulting in a large stress concentration, which causes the tap to break during use.
For example, improper heat treatment process. During the heat treatment of the tap, if it is not preheated before quenching, overheated or overfired, tempered not in time, and cleaned too early, it may cause the tap to crack. This is also an important reason why the overall performance of domestic taps is not as good as imported taps.
2. Improper selection of taps:
High-quality taps should be used for tapping parts with too much hardness, such as cobalt-containing high-speed steel wire taps, cemented carbide taps, and coated taps.
In addition, different tap designs are used in different workplaces. For example, the number, size, angle, etc. of the chip flute of the tap have an impact on the chip removal performance.
3. The tap does not match the processed material:
With the continuous increase of new materials and difficulty in processing, in order to meet this need, the variety of tool materials is also increasing. This requires choosing the right tap product before tapping.
4. The bottom hole diameter is too small:
For example, when machining M5×0.5 threads of ferrous metal materials, when using a cutting tap, a 4.5mm diameter drill should be used to make the bottom hole. If a 4.2mm drill bit is used to make the bottom hole by mistake, the cutting part of the tap will inevitably increase during tapping. , And then break the tap.
It is recommended to choose the correct diameter of the bottom hole according to the type of tap and the material of the tap.
5. Material problem of attacking parts:
The material of the tapping part is impure, and there are excessive hard spots or pores locally, which cause the tap to lose balance and break instantly.
6. The machine tool does not meet the accuracy requirements of the tap:
Machine tools and clamping bodies are also very important, especially for high-quality taps. Only a certain precision of machine tools and clamping bodies can exert the performance of the tap. It is common that there is not enough concentricity.
At the beginning of tapping, the tap positioning is incorrect, that is, the spindle axis is not concentric with the center line of the bottom hole, and the torque is too large during the tapping process, which is the main reason for the tap to break.
7. The quality of cutting fluid and lubricating oil is not good:
The quality of cutting fluids and lubricating oils has problems, and the quality of processed products is prone to defects such as burrs, and the service life will be greatly reduced.
8. Unreasonable cutting speed and feed rate:
When machining problems occur, most domestic users reduce the cutting speed and the feed rate, so that the pushing force of the tap is reduced, and the precision of the thread produced is therefore greatly reduced, which increases the surface roughness of the thread. The hole diameter and thread accuracy cannot be controlled, and problems such as burrs are of course more inevitable.
However, if the feed speed is too fast, the resulting torque is too large, which can easily cause the tap to break. The cutting speed during machine tapping is generally 6-15m/min for steel; 5-10m/min for quenched and tempered steel or harder steel; 2-7m/min for stainless steel; 8-10m/min for cast iron.
When the same material is used, the smaller tap diameter takes a higher value, and the larger tap diameter takes a lower value.
9. The operator’s technology and skills do not meet the requirements:
All of the above problems require the operator to make judgments or give feedback to the technicians.
For example, when processing blind hole threads, when the tap is about to touch the bottom of the hole, the operator does not realize that it is still fed at the tapping speed when the bottom of the hole is not reached, or the tap is broken by forced feeding when chip removal is not smooth. It is recommended that operators strengthen their sense of responsibility.
It can be seen from the above that there are many reasons for the breakage of the tap. Machine tools, fixtures, workpieces, processes, chucks and tools, etc. are all possible. You may never find the real reason just by talking about it on paper.
As a qualified and responsible tool application engineer, the most important thing is to go to the site, not just rely on imagination.
In fact, neither traditional tapping equipment nor expensive CNC equipment can solve the above-mentioned problems in principle. Because the machine cannot identify the working condition of the tap and the most appropriate torque required, it will only repeat the processing according to the preset parameters. Only when the machined parts are inspected with a thread gauge at the end will they be found to be unqualified, and at this moment it is too late to find out.
Even if it is found, it is useless. No matter how expensive the scrapped parts are, they have to be scrapped, and substandard products have to be thrown into defective products.
Therefore, in large enterprises, high-quality taps must be selected for processing large, expensive and precise workpieces.
So I want to introduce you the XINFA HSS Taps, please check the website to see more details:HSS Tap Manufacturers and Suppliers – China HSS Tap Factory (xinfatools.com)
Post time: Feb-19-2021